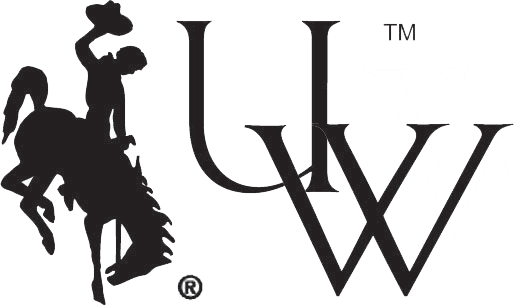
UW 3-27-20
The University of Wyoming’s Tyler Kerr never thought he and his team would be on the front lines of the COVID-19 battle.
With the nationwide spread of the coronavirus the last several weeks, medical supplies have become dangerously low, especially the demand for medical masks used by professionals to guard against the spread and protect against the virus.
Wyoming is not immune from COVID-19, with the number of confirmed cases increasing significantly in recent days. Already, some medical facilities in the state are facing medical supply shortages.
One of those facilities is Cheyenne Regional Medical Center (CRMC), whose medical workers reached out to Kerr for assistance and have requested at least 100 protective masks and 100 face shields.
Kerr — the UW makerspace coordinator in the Student Innovation Center (SIC), located in the new Engineering Education and Research Building — and his team are stepping up to the plate to help. They are producing 200 masks in this first round — 100 surgical facemasks by Monday, immediately followed by 100 face shields in the days following the first delivery.
All will be produced through the SIC’s 3D printers and laser cutters.
“We have been provided a unique opportunity to lend our equipment, resources and expertise to help stem the tide, flatten the curve and prevent spread of the virus, however the medical community asks us to,” Kerr says. “How often in our lives can we say that we have $1.4 million in state-of-the-art equipment made almost exactly for rapid prototyping purposes such as these? To do nothing with these resources was never really an option. This was our call to arms.”
To date, Kerr and his team have only made a few prototypes of a number of different facemasks and face shield designs to showcase to different health professionals. However, that changes this weekend when official production kicks off and runs around the clock to get the surgical masks and face shields sent to Cheyenne.
Health care facilities nationwide are facing severe shortages of personal protective equipment, says Dr. Jeff Chapman, CRMC chief medical officer.
“The biggest hurdle we are facing in health care facilities in the nation is shortages of personal protective equipment — specifically masks and face shields. As we look into the unknown of how long this pandemic will last or how many patients we could potentially have, we want to make sure we are as equipped and prepared as possible,” Chapman says. “It is a blessing that our community is able and willing to help out. We are especially grateful to the University of Wyoming for fulfilling this request, not only Cheyenne Regional Medical Center, but for other hospitals around the state.”
This is the first batch of masks Kerr and his team have produced, with more to come. The UW team is not charging any of the hospitals in the area for material or use of the machines.
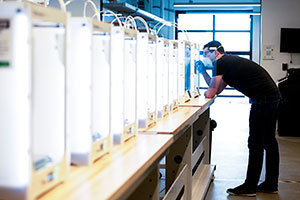
Ben Monger, an energy systems engineering student from Cheyenne, inspects one of the 3D printers that is producing one of the 100 surgical facemasks that will be donated to Cheyenne Regional Medical Center. (UW Photo)
“It is and will continue to be free,” Kerr says. “This is likely the first of many. Area hospitals have expressed interest in face shields we are producing, which are easy for us to make en masse.”
CRMC registered nurse Doug Berg initially made contact with Kerr for the request of the surgical masks.
“Doug is a prolific and enthusiastic maker in his own right. He had prototyped and printed a few models of the 3D masks we are printing and, ultimately, he came to us once he had shown the design to the CRMC leadership team for a stamp of approval,” Kerr says. “We feel confident that, with CRMC’s feedback, this design at its core level meets the rigorous health standards necessary to help stem the virus.”
The UW SIC team is making the face masks and face shields with ABS (acrylonitrile butadiene styrene), the same sort of plastic found in Legos, because it is more resistant to higher temperatures than more common plastics that a hobbyist 3D printer might work with at home. ABS also is easier to sterilize.
It takes approximately four hours to print one mask, Kerr says. He adds that his team is printing two masks — and two filter cartridges — per machine, hoping to squeeze three masks in to a build plate, which would take a cumulative 12 hours.
After the design step, the team prepares the file in a 3D printing program called a “slicer” or “slicing program” that divides the model into thousands of horizontal layers. The slicing program tells the 3D printer exactly how it should move the print head — called an extruder — in order to create each layer. The file then is sent with the instructions for the extruder over to the 3D printer.
“The slicer does all the hard thinking for us. We just tell it the parameters we want — not that much different than the decisions you make when printing out a paper document, just with a few extra choices,” Kerr says. “The best analogy we have found is to think of 3D printers like very smart hot glue guns. At its core, the 3D printer is simply using computer controls to move an extruder back and forth, left and right, up and down, as it ejects hot melted plastic out of a nozzle, like a hot glue gun melts glue sticks, one layer at a time.”
The molten plastic is cooled with fans the moment it comes out, and a layer-by-layer 3D model forms. The difference is that the printer’s nozzles are only approximately 0.4 millimeters (400 microns) wide, which means the team can print much higher resolution than glue gun nozzles can extrude hot glue.
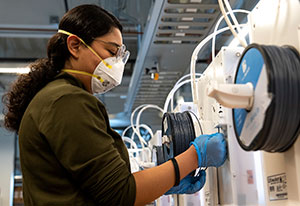
Ana Flores, a physics undergraduate from Guadalajara, Mexico, feeds a 3D printer with ABS (acrylonitrile butadiene styrene) filament that will produce one of the 100 plastic face shields to be given to the medical staff at Cheyenne Regional Medical Center early next week. (UW Photo)
His team is using six Ultimaker 3 Extended and two Ultimaker S5s devices to print the first batch of 100 masks, as well as two laser cutters to cut the face shield visors from thin plastic sheets.
The products being developed by the SIC team will serve as surgical masks and not the more advanced N95 masks that are now in high demand nationwide. Those masks are considered true respirators and are rigorously tested by the Food and Drug Administration for years before public use.
Jesse Evans, a computer science undergraduate researcher from Green River, developed the code to help speed up the 3D printing process in the SIC. Also assisting in the overall project are UW computer science Assistant Professor Lars Kotthoff and UW student Tyler Heckenlively, from Littleton, Colo.
On Kerr’s team are Victoria Evans, a pre-pharmacy student from Green River; Ana Flores, a physics undergraduate student from Guadalajara, Mexico; Shannon Linch, a chemical engineering student from Riverton; Ben Monger, an energy systems engineering student from Cheyenne; and Dee Retting, a journalism major from Colorado Springs, Colo.
Kerr says all the credit should go to Berg and the mask’s designers, Spencer Zaugg and Family Dentistry in Billings, Mont., for getting the project into the SIC team’s hands.
“We recognized that we could serve an important role to help produce custom parts or protective equipment locally, safely and efficiently in order to get crucial equipment in the hands of medical professionals rapidly during critical shortages,” Kerr says. “This was not our idea, but one that seemed to be borne out of the maker movement nationwide. We simply started paying attention to what others were doing, how other emergent tech centers were answering the call. It certainly feels like our duty to help however we can. There really wasn’t ever another option to sit idly by.”